Getting an eCommerce shop up and running is already stressful, but focusing all your resources on marketing leaves you vulnerable. To build a successful e-commerce business means that you’ll have to start thinking about logistics. That means figuring out how to cut warehouse costs and costs throughout your supply chain. But some mistakes are more common and costly than others. So, if you want to build a strong supply chain, it’s best to start with the biggest troublemakers.
Try Re-Organizing Your Warehouse…Just a Little
E-Commerce is all about variable costs. This includes COGS, packaging, shipping, labor, etc. Fortunately, variable costs are recurring and thus a great place to look to cut warehouse costs. Even if you only save a penny per package, those numbers add up.
Every order demands inventory, which means your pickers are constantly going to the shelves. So establishing and organizing a way to put inventory on shelves systematically will save you a fortune on labor in the long run. To test this, try moving a few medium-high volume items closer to your packaging center. After a few weeks of observation, evaluate whether or not this makes a difference. If so, start testing with other products.
Try New Picking Methods
One of the simplest strategies to cut warehouse costs is swapping picking methods. Some warehouses have a standard operating procedure while others do not. In either case, there is usually a better option out there. This is because mixing the different methods is often ideal. Here are some of the most common methods:
When a picker picks multiple orders on the same trip.
When a picker only picks one order at a time.
When each picker is assigned a zone to pick items from.
When each picker is assigned to a zone but will pass single orders or orders in bulk from zone-to-zone.
When a picker places products directly into a shipping container (such as a box or parcel). This is a great way to cut warehouse costs.
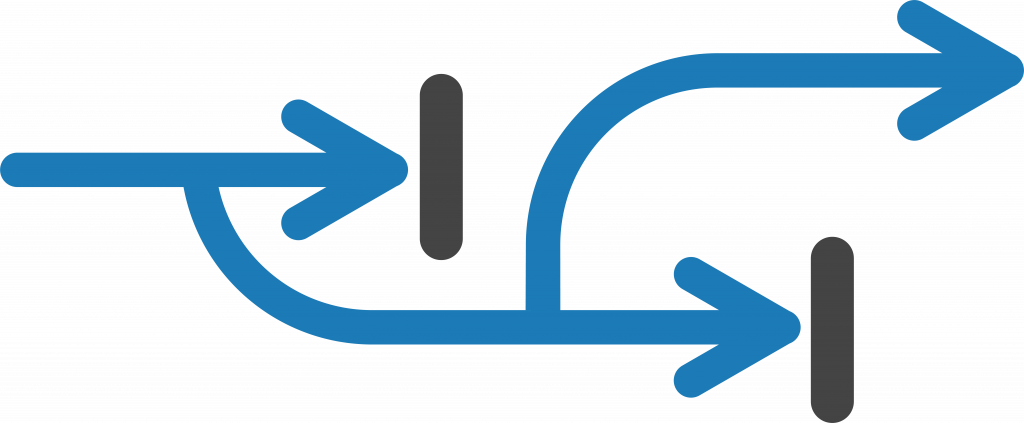
Try Creating Inbound Workflows
Warehouse Management is all about controlling the environment from entry to exit. If inventory arrives at the warehouse without a putaway protocol, then you lose control. It doesn’t matter if the product is a return, replenishment, exchange, or new inventory – there should always be a process. Here are some specifics to address:
- Where does hurt inventory go?
- Is there a different process for replenishments, returns, and exchanges?
- Where do we hold inventory before it gets put away?
- Who is in charge of the putaway process?
- How do you decide what inventory goes where?
- How do you track all of this information?
Consider Cross-Docking and Dropshipping
Cross Docking
AKA Just in Time Fulfillment. You receive an order on your inbound dock and immediately take it your outbound dock.
Dropshipping
When a different warehouse ships the order to the consumer directly.
The three major cost points for fulfillment are shipping, labor, and warehouse space. Cross Docking and Drop Shipping can alleviate some of these pain points. Shipping and product costs may be higher, but you can save on labor and storage. Plus, you can utilize some of those extra resources and offer fulfillment services to new clients.
Communicate with suppliers and DCs to see whether or not these are options for you. Like picking methods, the optimal solution is likely a mix. So, it will take some tweaking but can ultimately make a dent in cutting warehouse costs.
Conclusion
There is a lot of pressure on the global supply chain today. eCommerce is a young industry and this volume of fulfillment is too. As the industry continues in flux the only thing we know for certain is that cost-cutting is on everyone’s mind. In times of pressure, humans tend to act irrationally. Some companies will spend hundreds of thousands of dollars in order to cut warehouse costs, but it doesn’t have to be so complicated. Instead, start with the small things to control your environment. Not only can this make an impact, but it will also position you better if you choose to take further action.
0 Comments