In the bustling, multifaceted environment of a warehouse, accuracy and precision are paramount. With numerous processes happening simultaneously, from receiving goods to dispatching them, every single procedure must be flawless.
One of the most critical areas where precision is non-negotiable is the picking process. A mis-pick, an incident where a wrong item gets picked for an order, can create a ripple effect leading to incremental costs affecting not just the warehouse operations but the company’s rapport with its clients as well. Warehouse mis-picks are easily avoidable when using the right techniques and technology to supplement your everyday operations.
In this short guide, we’ll delve deeper into the intricacies of warehouse mis-picks, their underlying costs, and potential strategies for minimizing mis-picks.
Understanding Mis-picks in a Warehouse Environment
In essence, a mis-pick occurs when an employee selects the incorrect product during the order-picking process. This simple error can significantly disrupt the flow of operations within the warehouse, leading to additional costs and potential customer dissatisfaction.
The Pervasiveness of Mis-picks
Warehouse mis-picks aren’t anomalies in a warehouse environment. Given the sheer volume of operations, especially in eCommerce where the average order contains 3 units, human errors are not just possible, they are probable.
In warehouses without strategies in place to reduce the recurrence of mis-picks, significant associated costs will come along.
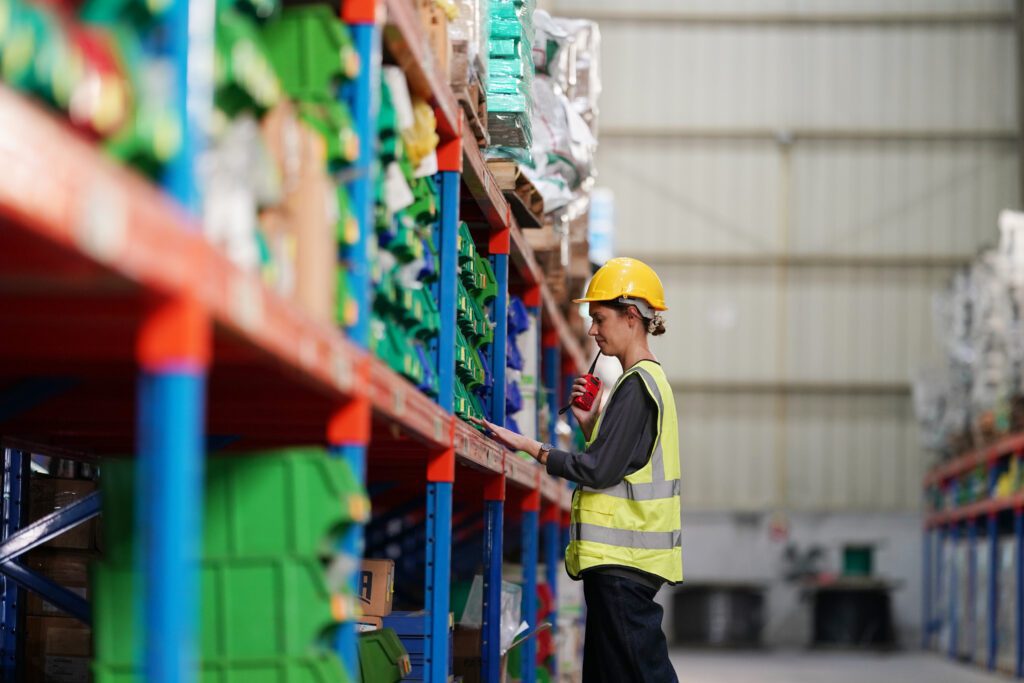
The Unseen Costs of Warehouse Mis-picks
At first glance, a mis-pick might seem like a minor inconvenience. However, when you start to unpack the repercussions of this seemingly small mistake, you begin to understand its true cost. These costs aren’t confined to tangible ones; they can extend to intangible areas like customer satisfaction and business reputation.
Labor Costs
Every error made in the picking process represents an investment of time, effort, and resources that did not result in value. Identifying the mistake, rectifying it, re-picking the correct item, and repacking the order, all entail additional labor costs. It’s like paying twice for work that should have been done correctly the first time.
Shipping Costs
If the mis-picked item reaches the customer, it will likely need to be returned and replaced with the correct item. This doubles the shipping cost for the affected order and introduces additional complexities into the equation, such as processing returns, which can be a complex and time-consuming task.
Impact on Customer Satisfaction
The value of customer satisfaction cannot be overstated in the age of online shopping, where consumers have a plethora of options at their disposal. A single mis-pick can lead to a dissatisfied customer, tarnishing the customer’s shopping experience, and potentially damaging your reputation if the customer shares their negative experience online.
Lost Sales and Business Opportunities
A dissatisfied customer may opt to shop elsewhere in the future, translating to lost sales for your business. Additionally, mis-picks can lead to inventory inaccuracies, which might result in out-of-stock situations, further leading to missed sales opportunities.
Strategies for Minimizing Warehouse Mis-picks
Given the high costs associated with warehouse mis-picks, it’s essential for businesses to take proactive measures to minimize their occurrence.
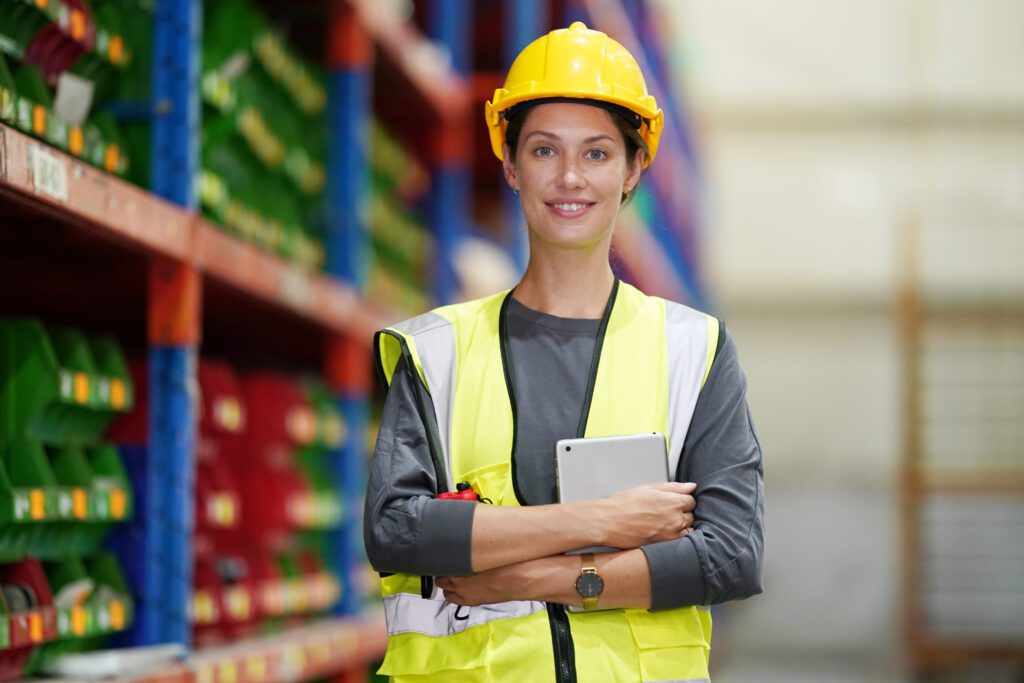
Investment in Employee Training
The importance of well-trained staff in a warehouse environment cannot be overstated. Regular training updates on picking procedures can help your team stay keen to best practices and significantly reduce the risk of mis-picks.
Leveraging Technology
Warehouse management systems (WMS), such as Shipedge, play a critical role in minimizing mis-picks. These systems, armed with features like real-time inventory tracking and barcode scanning, drastically improve the accuracy of the picking process, thereby reducing the risk of mis-picks.
One feature, in particular, has helped users of Shipedge ensure that their warehouse team is selecting the right item as they pick it. When laborers use the Shipedge app on their Android devices, an image will appear to confirm that the item they’ve picked is correct.
In addition to real-time inventory tracking, barcode scanning, and picking confirmation, advanced WMS solutions also provide in-depth insights into warehouse operations, helping identify potential problem areas and enabling continuous improvement.
Discover how our WMS can improve your business
Optimizing Warehouse Layout
A well-structured and logically organized warehouse can facilitate a smooth picking process. Grouping similar items together and placing high-demand items in easily accessible locations can reduce picking times and minimize the likelihood of errors.
Over the past decade, Shipedge has been conducting warehouse research to determine the best way to organize a warehouse. Learn more about the best way to set up your warehouse for success in the short video below:
Implementing Regular Audits
Periodic checks on the accuracy of your picking process can help identify recurrent issues, allowing you to address them before they snowball into larger problems. By using a WMS, you can easily check the picks-per-hour of each warehouse team member, as well as their picking accuracy. With the use of Shipedge’s app, picking errors should be near 0%, and picks-per-hour should dramatically increase when the warehouse is organized properly. Shipedge’s WMS will automatically route pickers in the most efficient way depending on the locations of the items waiting to be picked, and the particular needs of the company.
Utilizing Advanced WMS Solutions like Shipedge
Implementing a robust Warehouse Management System like Shipedge can be a game-changer for minimizing mis-picks. Designed with user-friendliness and functionality in mind, Shipedge is equipped with features like real-time inventory tracking and barcode scanning, ensuring that the correct items are picked each time, thereby drastically reducing the chance of mis-picks.
Moreover, with a systematic record-keeping feature, Shipedge ensures transparency and traceability, providing a clear trail of which employee picked and packed each order. This not only instills accountability among the workforce but also allows for quick identification of the warehouse mis-pick and rectification of errors, preventing the costly event of a customer receiving an incorrect item.
While it’s imperative to note that even with the best systems in place, human errors can still occur. Having the right tools significantly reduces the likelihood of warehouse mis-picking and offers an effective strategy to mitigate the impact of these mistakes.
Final Thoughts
Understanding the costs associated with warehouse mis-picks is the first step towards developing a strategy to mitigate them. By investing in proper staff training, leveraging technology, optimizing the warehouse layout, and implementing regular audits, you can dramatically reduce these costs. Minimizing mis-picks with an advanced WMS solution like Shipedge can be pivotal in this aspect, offering features that enhance accuracy, improve efficiency, and ultimately, support customer satisfaction. Every warehouse mis-pick avoided is a step towards improved operational efficiency and a better bottom line.
Discover how our WMS can improve your business
0 Comments