There are many areas of warehouse operations that warehouse managers can point to for data points, but which ones are the most important to pay attention to?
Effective warehouse management is crucial for the success of any logistics or eCommerce business. Tracking and measuring the right key performance indicators (KPIs) can provide valuable insights into the efficacy of warehouse operations. This article lists some of the top KPIs for warehouse managers to know.
Picks Per Hour
One of the top key performance indicators (KPIs) you can identify in your Warehouse Management System (WMS) is picks per hour.
Picks per hour is a warehouse KPI that measures the average number of items picked by a warehouse worker per hour. Increasing picks per hour can lead to greater efficiency and lower labor costs. A WMS like Shipedge can provide real-time data on picks per hour for each user, allowing warehouse managers to track worker productivity and identify opportunities for improvement.
Warehouse managers can use this data in the WMS to analyze picking processes and identify areas where improvements can be made, such as implementing more efficient picking methods, optimizing warehouse layout, or providing additional training to workers. By focusing on increasing picks per hour, warehouse managers can improve overall efficiency and reduce labor costs.
READ MORE: 7 Effective Picking Methods for Maximizing Warehouse Efficiency
Order Accuracy Rate
Going hand-in-hand with picks per hour, the order accuracy rate measures the percentage of orders that are picked, packed, and shipped without errors. A high order accuracy rate is essential for maintaining customer satisfaction and minimizing the costs associated with returns and replacements. Using a WMS like Shipedge, you can track your order accuracy rate and identify areas where improvements can be made.
Warehouse managers can use WMS data to analyze the causes of order inaccuracies, such as picking errors, packing mistakes, or data entry issues. By addressing these problems, warehouse managers can improve their order accuracy rate and reduce the costs associated with incorrect orders.
Return Rate
The return rate measures the percentage of shipped orders that are returned by customers. A high return rate can indicate order accuracy, product quality, or customer satisfaction issues. Warehouse managers can use data found in their warehouse management software to monitor return rates and identify the root causes of returns, such as picking errors, product defects, or inaccurate product descriptions.
Around 30% of outbound shipments turn into eCommerce returns. By addressing the abovementioned issues, warehouse managers can reduce return rates, minimize the costs associated with returns, and improve customer satisfaction.
Discover how our WMS can improve your business
Inventory Turnover
Inventory turnover is a warehouse KPI that measures how many times your inventory is sold and replaced over a given period. A high inventory turnover rate indicates that your products are selling quickly, which is generally a positive sign. However, it can also signal potential issues with stockouts or overstocking.
A warehouse manager may consider relocating low inventory turnover products towards the back of the warehouse and moving high turnover rate products towards the front to reduce the time it takes for a picker to travel across the warehouse. Seasonality may affect the rate at which inventory turns over, so be aware of upticks in orders for certain products around the holidays.
An eCommerce brand using a WMS for its own warehouse may use an inventory turnover rate to recognize which products may be overstocked or not selling well. In this case, the brand may consider implementing targeted promotions or discounting slow-moving items.
Order Cycle Time
Order cycle time measures the average time it takes to process an order, from the moment it is received until it is shipped to the customer. Reducing order cycle times is essential for meeting customer expectations and maintaining a competitive edge in the eCommerce industry.
Using data from your WMS, users can monitor order cycle times and identify areas where improvements can be made. Some actions that may improve warehouse efficiency include implementing a more streamlined picking and packing process, automating order processing steps, or optimizing warehouse layout to minimize travel times.
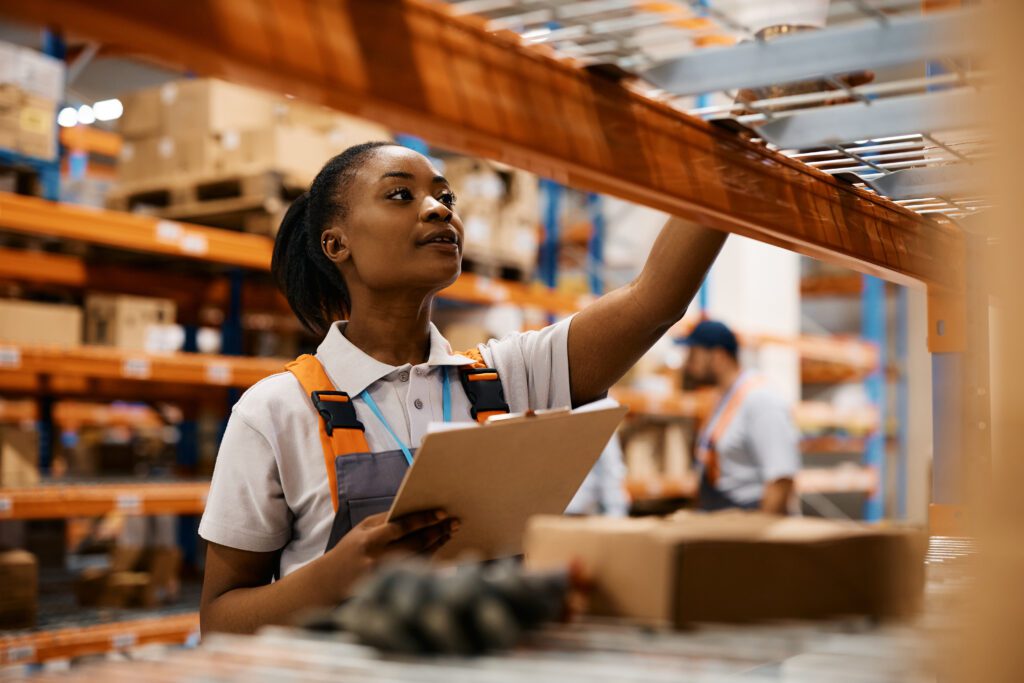
On-Time Shipments
On-time shipments measure the percentage of orders that are shipped on or before the promised delivery date. Meeting customer expectations for timely delivery is critical for maintaining customer satisfaction and building a positive reputation in the market.
In certain cases, having orders leave the warehouse within a day is the only option. For example, a company fulfilling through Amazon must fulfill Prime orders to arrive on the end-consumers doorstep within 2 days. If this condition is not met, sellers could be penalized or even removed from the selling channel.
Managers can use this particular KPI to address any bottlenecks or issues that may be causing delays such as the picking and packing process, or potential staffing shortages. Managers may even collaborate with carriers to improve shipping times, or consider diversifying their shipping carrier strategy and implementing best-rate shipping for cheaper shipments.
Backorder Rate
The backorder rate is a warehouse KPI that measures the percentage of orders that cannot be fulfilled due to insufficient inventory. A high backorder rate can lead to customer dissatisfaction and lost sales, so it is essential to keep this rate as low as possible.
This warehouse KPI could help identify trends that may indicate issues with inventory management. By addressing these issues, warehouse managers can reduce backorder rates and improve customer satisfaction.
Capacity Utilization
Capacity utilization is a 3PL warehouse KPI that measures the percentage of available warehouse space that is being used for storage. Efficient use of warehouse space is essential for maximizing profitability and minimizing overhead costs.
Warehouse managers can use WMS data to monitor capacity utilization and identify trends that may indicate issues with warehouse space management. For example, consistently low capacity utilization rates may suggest that products are overstocked or not selling well. In this case, warehouse managers can adjust ordering patterns, implement targeted promotions, or consider offsite storage options. Conversely, if capacity utilization is consistently high, it may be necessary to expand warehouse space, reorganize storage locations, or invest in vertical storage solutions to optimize the use of available space.
READ MORE: Optimize Your Warehouse Layout for Maximum Efficiency and Productivity
Dock to Stock Time
Dock-to-stock time measures the average time it takes for received goods to be put away in their designated storage locations. Efficient dock-to-stock processes can help minimize delays in order processing and reduce the risk of errors in inventory management.
Warehouse managers can use WMS data to monitor dock-to-stock times and identify opportunities for improvement. This may include implementing more efficient receiving processes, such as using barcode scanning technology for faster and more accurate putaway or reorganizing the warehouse layout to minimize the travel distance between receiving areas and storage locations.
Average Cost Per Order
The average cost per order is a warehouse KPI that measures the total costs associated with processing an order, including labor, materials, and overhead. By reducing the average cost per order, warehouse managers can improve profitability and gain a competitive advantage in the market.
Warehouse managers can use WMS data to analyze the components of their average cost per order and identify areas where improvements can be made. This may include optimizing labor allocation, implementing more efficient picking and packing processes, or negotiating better rates with suppliers and carriers.
Discover how our WMS can improve your business
Using Warehouse KPIs with Shipedge
Shipedge offers the tools you need to identify Key Performance Indicators specific to your business and how operations are run specific to your industry.
By monitoring and analyzing the essential warehouse KPIs discussed in this article, warehouse managers and operations managers can gain valuable insights into their warehouse’s performance and make data-driven decisions to improve efficiency, reduce costs, and enhance customer satisfaction. Implementing a Warehouse Management System like Shipedge can help warehouse managers track and optimize these warehouse KPIs, ensuring that their warehouse operations are performing at the highest level possible.
By focusing on warehouse KPIs and leveraging the powerful features of a WMS, warehouse managers can drive continuous improvement and maintain a competitive advantage in the ever-evolving world of logistics and eCommerce. The proper use of warehouse KPIs allows for the identification of areas in need of improvement, enabling managers to allocate the proper resources and implement changes that will yield the greatest benefits.
The warehouse KPIs discussed in this article are just a starting point for developing a complete understanding of warehouse performance. With the help of a WMS like Shipedge, warehouse managers can track additional KPIs that are specific to their unique operations and industry. As managers become more adept at utilizing warehouse KPIs, they will be better equipped to respond to changes in the market and make informed decisions that will ensure the ongoing success of their business.
To find out more about how Shipedge can help identify warehouse KPIs used frequently by warehouse managers, reach out to a solutions engineer on our Get Started page.
0 Comments