In today’s competitive business landscape, efficient warehouse management is crucial for companies to stay ahead. One aspect that significantly impacts a warehouse’s operational costs is shipping expenses.
Finding ways to reduce shipping costs while ensuring timely and reliable delivery is a priority for businesses. To address this challenge, we present a comprehensive guide to reducing shipping costs in your warehouse. By implementing the tips below, you can optimize various aspects of your shipping operations, improving efficiency, reducing expenses, and enhancing customer satisfaction.
Ultimately, meet Shipedge WMS, the warehouse software management system that will help your company add all these essential features to your business.
8 Tips to Reduce the Shipping Costs of Your Warehouse
If you prefer to go into one of the mentioned topics, use the summary below to improve the navigation.
1 – Optimize Inventory Management
Optimizing warehouse management involves implementing strategies and techniques to improve warehouse efficiency and production operations, for example:
- Streamlining processes: simplifying workflows, eliminating redundancies, and improving efficiency to reduce costs, minimize errors and enhance overall performance. It involves optimizing inventory organization, implementing tracking systems such as barcode scanning, and utilizing automation technologies for faster order fulfillment and improved customer satisfaction.
- Organizing inventory: arranging goods systematically within a warehouse, ensuring easy accessibility, efficient storage, and accurate tracking. Organizing inventory will improve operational efficiency, minimizes search time, prevents inventory discrepancies, and maximizes space utilization, resulting in cost savings and enhanced customer service.
- Optimizing picking and packing operations: focuses on improving the speed, accuracy, and efficiency of selecting and packaging items for shipment. This procedure involves optimizing workflows, utilizing technology, and implementing best practices to reduce errors, increase throughput, and enhance order fulfillment, resulting in improved customer satisfaction and cost savings.
- Utilizing automation technologies: using automated technologies such as automated conveyor systems and inventory management software. This improves productivity, reduces human errors, speeds up processes, and enhances overall warehouse efficiency, leading to cost savings and improved customer satisfaction.
The goal is to reduce shipping costs, minimize errors, improve order fulfillment speed, and maximize overall warehouse performance. By optimizing warehouse management, businesses can enhance customer satisfaction, reduce operational expenses, and gain a competitive edge in the market.
Discover how our WMS can improve your business
2 – Implement Automated Picking and Packing
Picking and packing are crucial processes in warehouse operations for efficient order fulfillment and safe delivery of products.
Picking involves:
- Retrieving items: locating and obtaining specific products from storage in a warehouse, is essential for timely order fulfillment and accurate inventory management.
- Selecting the most efficient method.
While packing ensures goods are securely packaged with appropriate materials and labeled for transportation and storage.
Preparing orders for shipment: securely packaging them, labeling them with shipping information, and arranging the most cost-effective shipping method. Opting for the best shipping rate possible minimizes costs while ensuring timely delivery, contributing to profitability and customer satisfaction.
To optimize these processes, automated packing and picking can be implemented. This technology helps:
Reduce errors, improve efficiency, and decrease labor costs. With the assistance of software, optimized pick paths can be generated, orders can be consolidated, and barcode scanning capabilities can be utilized, ensuring accurate and speedy order fulfillment.
By integrating automated picking and packing systems into warehouse operations, businesses can achieve streamlined processes, enhanced productivity, and improved customer satisfaction. These advancements contribute to efficient order processing, reduced errors, and cost savings, ultimately leading to a more competitive and successful warehouse management approach.
READ MORE: 7 Effective Picking Methods for Maximizing Warehouse Efficiency
3 – Utilize Real-Time Data and Analytics
Real-time data and analytics can decrease shipping costs in a warehouse by providing valuable insights into various aspects of the shipping process. With the ability to do data analysis in real time, businesses can identify inefficiencies, bottlenecks, and areas of improvement that directly impact shipping costs.
This allows them to:
- Make data-driven decisions: using real-time data and analytics to inform and guide business choices, ensuring optimal outcomes based on accurate insights, leading to improved efficiency and cost savings.
- Optimize workflows: analyzing and improving the sequence of tasks, resource allocation, and communication within a process based on real-time data and analytics. This leads to increased efficiency, reduced costs, and improved overall performance in warehouse operations, including shipping processes.
- Streamline processes: By leveraging real-time data and analytics, businesses can identify sections to improve and implement changes to streamline shipping processes, leading to smoother operations and enhanced cost-effectiveness.
- Implement cost-saving measures: such as route optimization, carrier selection, and inventory management.
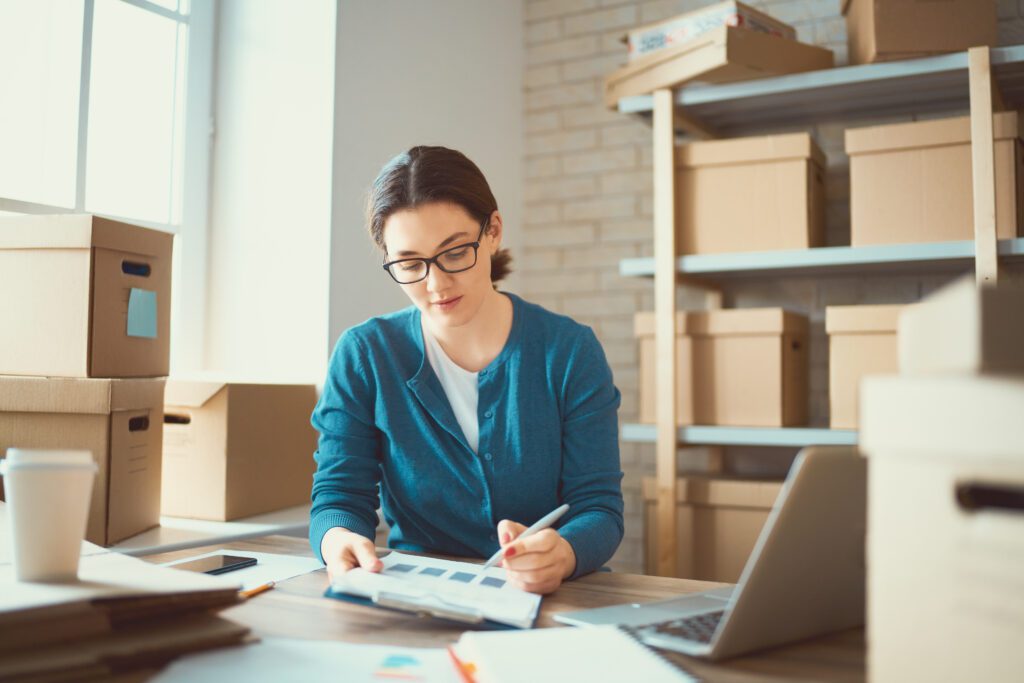
READ MORE: 10 Must-Have Features in a Modern Warehouse Management System
Shipedge’s WMS (Warehouse Management System) is a comprehensive software platform that offers advanced features for warehouse operations, including inventory management, order fulfillment, and shipping management. Shipedge’s WMS provides real-time data and analytics capabilities, allowing businesses to monitor and analyze key shipping metrics, identify cost-saving opportunities, and optimize their shipping operations. By leveraging the features and functionalities of Shipedge WMS, businesses can streamline their shipping processes, reduce errors, and ultimately decrease shipping costs while improving overall operational efficiency.
Discover how our WMS can improve your business
4 – Implement Best Rate Shipping
Best rate shipping, also referred to as best rate possible (BRP), refers to the most cost-effective and efficient shipping option that considers factors such as:
- Package size
- Weight
- Destination
- Delivery timeline
Warehouse management software integrates with shipping carriers’ systems to compare rates and select the most economical options, ensuring timely and reliable delivery while minimizing shipping expenses. This integration allows businesses to optimize their shipping choices, improving profitability and customer satisfaction.
READ MORE: How Best Rate Shipping Supports Omnichannel Retail Strategies
5- Optimize Packaging and Dimensional Weight
Proper packaging practices like cartonization can minimize shipping costs and enhance order fulfillment efficiency. Warehouse management software may incorporate features like:
Dimensional weight calculations and suggestions for appropriate box sizes, optimizing shipping expenses.
Reducing excess packaging and optimizing dimensions based on automated analysis avoids unnecessary dimensional weight charges, decreasing shipping expenses. Implementing cartonization in your warehouse workflow ensures each item’s most efficient and cost-effective packaging, contributing to overall cost savings and improved fulfillment efficiency.
Discover how our WMS can improve your business
6 – Implement Batch Processing and Order Batching
Batch picking, while not directly reducing the total number of shipments, offers significant benefits regarding order fulfillment time. By combining multiple orders or batch processing orders, picking routes can be optimized, resulting in more efficient operations.
Warehouse management software is important in group orders based on factors like shipping address proximity or products ordered together. Through consolidating orders, businesses can effectively reduce shipping costs by minimizing the number of packages and optimizing the routes taken for delivery.
7- Streamline Returns Management
Efficiently managing product returns is crucial for minimizing shipping costs associated with return shipments.
By leveraging the robust features of your warehouse management software, you can automate and streamline the returns process, resulting in timely processing and reduced shipping expenses. The software can provide:
- A centralized system: for handling return requests;
- Tracking returned items.
- Initiating appropriate actions: such as restocking or replacement.
This automation helps expedite the returns process, reducing the time taken for inspections, assessments, and subsequent actions.
Additionally, the software can facilitate communication between the warehouse and customers, providing real-time updates on return status, refund processing, and shipping instructions.
By optimizing the returns management process, businesses can improve:
- Operational efficiency;
- Reduce the likelihood of errors.
- Minimize unnecessary shipping costs associated with returns.
This increases customer satisfaction and contributes to overall cost savings and a streamlined warehouse operation.
Discover how our WMS can improve your business
8- Integrate with Transportation Management Systems (TMS) or ERP systems
If your warehouse management software (WMS) can integrate with an ERP system or Transportation Management System (TMS), it can provide several advantages. By utilizing these systems, businesses can achieve end-to-end visibility and optimization of transportation operations.
This allows for consolidation shipments, selecting the most cost-effective carriers, and streamlining shipping processes.
The integration enables seamless data sharing between the WMS and TMS/ERP, allowing for more efficient coordination and decision-making. This ultimately leads to reduced shipping costs, improved shipment planning, and enhanced overall logistics management.
Effectively managing shipping costs in your warehouse is crucial for optimizing profitability and customer satisfaction. You can significantly improve your shipping operations by implementing the right strategies and leveraging advanced warehouse management software like Shipedge WMS.
READ MORE: Warehouse Management System Software: A Starting Guide
Shipedge WMS offers features such as real-time data and analytics capabilities, automation of picking and packing processes, integration with shipping carriers’ systems for best-rate shipping, optimization of packaging and dimensional weight, batch processing, streamlined returns management, and integration with TMS or ERP systems. Utilizing these capabilities can reduce shipping expenses, improve order fulfillment efficiency, and gain a competitive edge in the market. Consider adopting Shipedge WMS to enhance your business and achieve cost savings in your warehouse operations.
Discover how our WMS can improve your business
0 Comments