The eCommerce sector’s relentless pace and unforgiving competitive landscape have amplified the importance of a flawless fulfillment process. Any error in this crucial operation can dent customer satisfaction, tarnish a brand’s reputation, and erode the bottom line. As such, minimizing fulfillment errors has become an urgent priority for businesses.
Shipedge, an industry leader in innovative logistics solutions, offers an array of tools to help businesses minimize these mistakes and raise their fulfillment standards. This comprehensive guide examines the best practices for reducing fulfillment errors and the ways Shipedge’s platform aids in achieving this goal.
The Power of Automation in Reducing Fulfillment Errors
Automation is a linchpin in the quest for reducing fulfillment errors. The less manual involvement in the fulfillment process, the lower the possibility of human error. Automation streamlines operations and cuts down the risk of inaccuracies.
Shipedge has been an avid proponent of automation in order fulfillment. Our suite of solutions is designed to augment efficiency, precision, and productivity. One of the standout features of Shipedge’s offering in this respect is the Barcode Scanning tool for accurate picking.
READ MORE: The Role of Warehouse Automation in Reducing Operational Costs
Barcode Scanning for Accurate Picking
Picking is one of the most critical stages in the fulfillment process, and it’s also one of the stages most prone to errors. The repercussions of picking errors are wide-ranging and damaging: they can result in returns, customer dissatisfaction, and a host of downstream problems. Shipedge’s Barcode Scanning feature ensures that each picking operation is faultless.
The Barcode Scanning tool verifies that the correct item is picked every time. By confirming the match between the item barcode and the order information, the system guards against potential errors. This drastically reduces the possibility of picking mistakes and helps maintain a smooth, efficient fulfillment operation.
Regular audits and cycle counting are an integral part of maintaining accurate inventory. Miscounts and oversights during these operations can lead to picking and packing errors. Incorporating a regular schedule for these procedures is a necessary strategy for reducing fulfillment errors.
READ MORE: 7 Effective Picking Methods for Maximizing Warehouse Efficiency
Inventory Accuracy with Shipedge
Shipedge’s robust Warehouse Management System (WMS) is equipped with features to enable regular audits and cycle counting. With these tools at your disposal, you can ensure your inventory data remains accurate and up-to-date. Regular audits and cycle counting minimize the likelihood of discrepancies and errors in picking and packing, enhancing overall warehouse efficiency.
The Advantage of Real-Time Inventory Tracking
Another tool for reducing fulfillment errors is real-time inventory tracking. With the ability to access up-to-the-minute inventory data, businesses can prevent issues such as overselling or underselling. Accurate, real-time inventory tracking also enables more precise picking, further minimizing the risk of fulfillment errors.
Shipedge’s Real-Time Inventory Management
Available in the WMS, Shipedge’s real-time inventory tracking system provides a live snapshot of the available inventory at any given moment. This feature allows for accurate forecasting, helping businesses avoid scenarios where products are either oversold or undersold due to outdated inventory data. By keeping a real-time eye on inventory levels, you can prevent fulfillment errors due to discrepancies in inventory data.
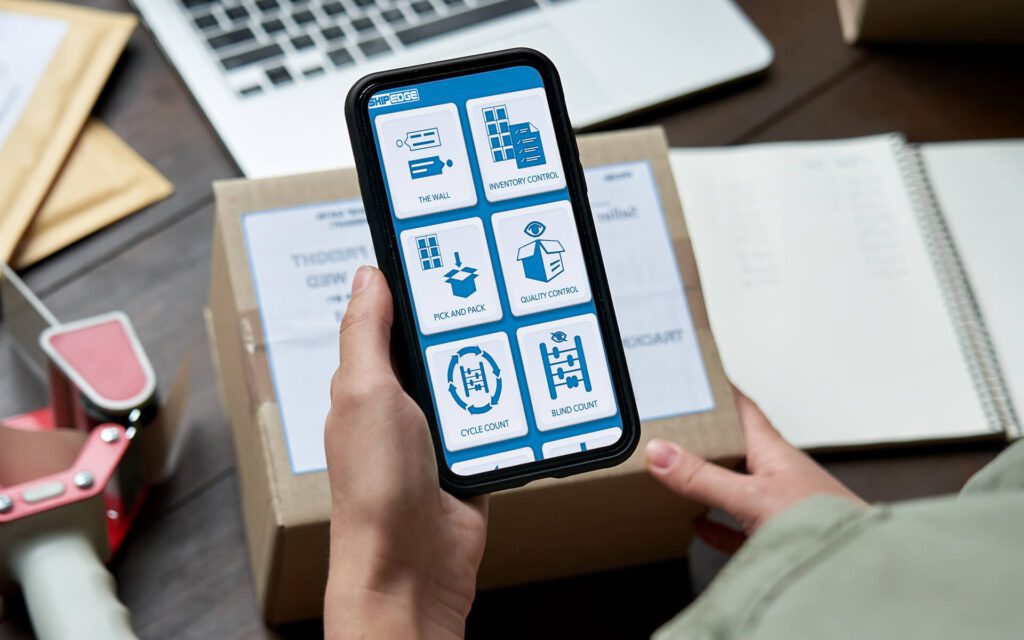
Effective Reverse Logistics: A Crucial Strategy in Minimizing Fulfillment Errors
While the primary focus should be on preventing fulfillment errors, it’s equally crucial to have a plan in place for when errors do occur. An effective reverse logistics strategy is instrumental in mitigating the impact of these mistakes, ensuring that returned products are promptly and efficiently processed and reintegrated into inventory.
Reverse Logistics with Shipedge
Shipedge’s robust Order Management System (OMS) features a streamlined reverse logistics process. This procedure ensures quick turnaround times for returned products, minimizing disruptions to your inventory levels and overall operations. The automation of this process not only speeds up the return process but also reduces the potential for errors in restocking, leading to more accurate inventory and smoother operations.
Discover how our WMS can improve your business
Harnessing Data to Minimize eCommerce Fulfillment Errors
The use of data analytics to gain insights into fulfillment operations can significantly help minimize errors. By tracking and analyzing performance metrics, businesses can identify patterns, bottlenecks, and areas prone to mistakes, thereby crafting strategies to address these issues.
Data Analytics with Shipedge
Shipedge’s platform is equipped with powerful analytics tools that provide real-time, actionable data. By tracking various metrics such as order processing times, return rates, and picking accuracy, businesses can gain a clearer picture of their fulfillment operations’ effectiveness. This data-driven approach allows for constant improvement and error reduction in the fulfillment process.
Discover how our WMS can improve your business
Enhancing Communication and Collaboration
Effective communication and collaboration within the warehouse team are essential in minimizing fulfillment errors. Clear communication about tasks, roles, and responsibilities ensures that every team member understands what’s expected of them, reducing the chances of missteps.
Collaborative Tools from Shipedge
Shipedge’s platform offers a suite of collaborative tools designed to enhance team communication and collaboration. Its WMS and OMS solutions allow for seamless information sharing, ensuring that every team member has access to the data and instructions they need to perform their roles efficiently and accurately. This fosters a culture of collaboration and accountability, which is crucial in reducing fulfillment errors.
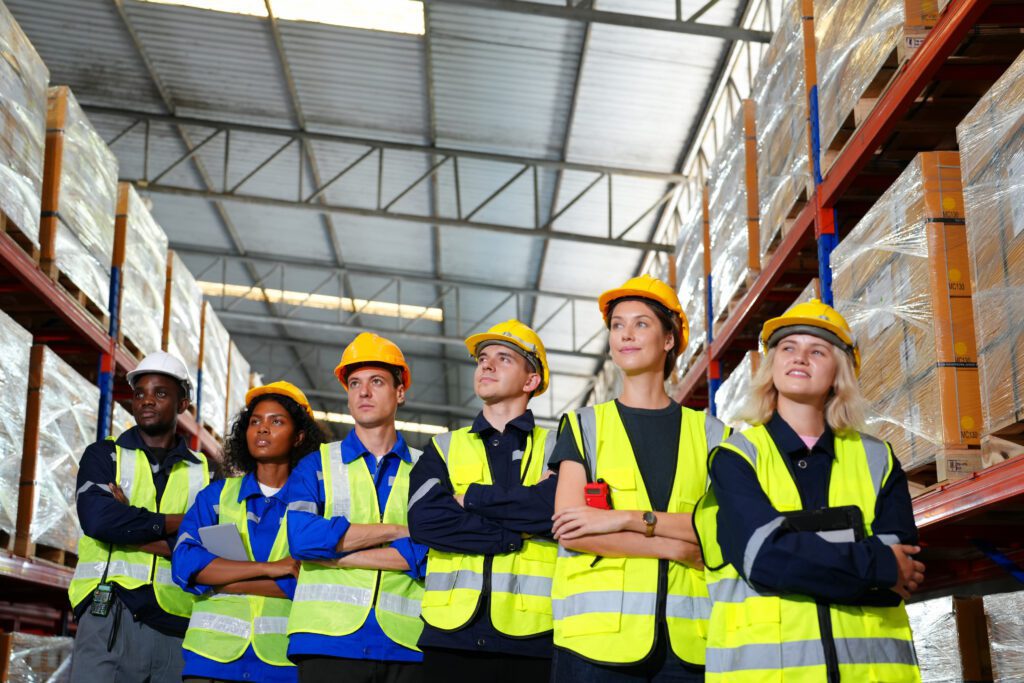
Training and Continuous Improvement
No system or strategy can replace the value of well-trained personnel in the warehouse. Providing regular training to staff, emphasizing the importance of accuracy, and promoting a culture of continuous improvement are crucial strategies for minimizing fulfillment errors.
Training and Support with Shipedge
At Shipedge, we believe in empowering businesses and their teams. To this end, we offer extensive training and support for new users of our WMS or OMS software solutions, ensuring that teams have the necessary skills and knowledge to minimize eCommerce fulfillment errors. Additionally, you can view our roadmap at any time to see what’s new and upcoming.
Part of our training includes videos on how to navigate the software, and a team of technical account managers to configure the software’s settings specific and customized to your needs. To learn more about our implementation process, read more here.
Discover how our WMS can improve your business
Conclusion
Reducing fulfillment errors is crucial in today’s competitive eCommerce landscape. Through automation, accurate inventory tracking, effective reverse logistics, data analytics, enhanced communication, and continuous training, businesses can significantly minimize these errors.
Shipedge’s suite of solutions provides the tools necessary for these strategies, empowering businesses to enhance their fulfillment accuracy and efficiency, ultimately leading to improved customer satisfaction and business growth in the eCommerce sector.
0 Comments